Forensics
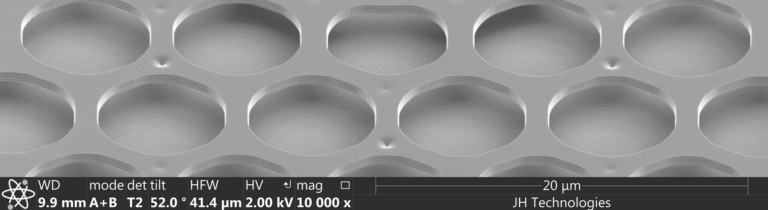
Crime labs make heavy use of optical imaging systems. Imaging is used to identify materials, identify human characteristics, or tie a weapon to a crime. There are six major crime lab areas, which use both macro and micro-optical imaging systems: DNA/Biology, Firearms/Toolmarks, Trace Evidence Chemistry/drug ID, fingerprints, footprints, and questioned documents. Both macro and micro imaging systems are used.
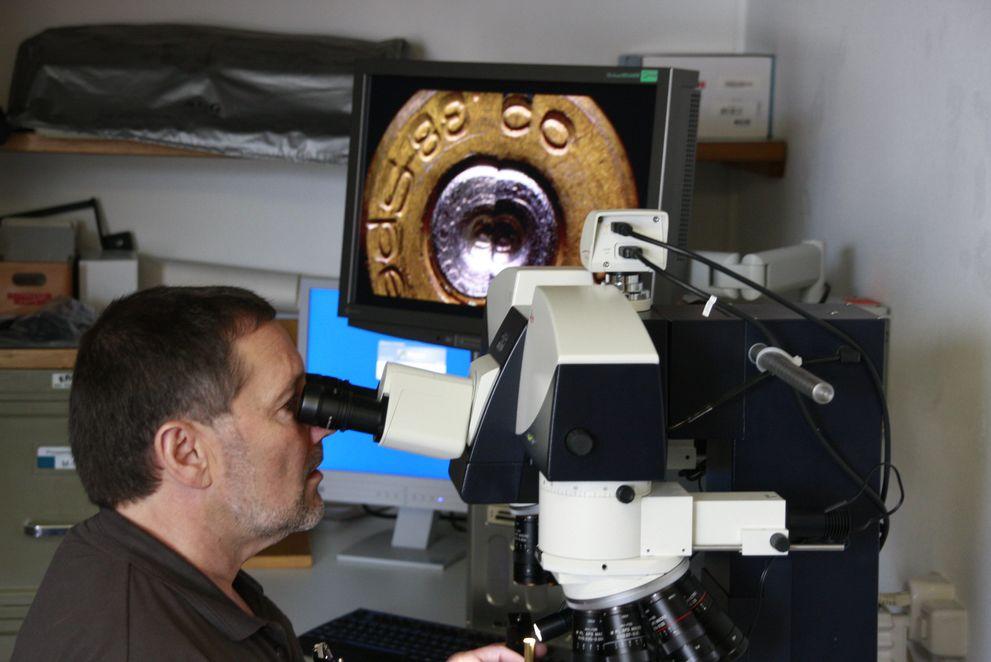
Related Blogs
Tariff Policy Simplified: Stability, Transparency, and Trust
Recent Blogs JHT Tariff Policy: Stability, Transparency, and Trust Stability,...
Read MoreDemonstration Equipment: Beating The Tariff Trap
Recent Blogs Demonstration Equipment: Beating the Tariff trap In a...
Read MoreThe Case of the Missing SEMs: A Story of Quick Thinking, Teamwork & Tech Recovery
Recent Blogs The Case of the Missing SEMs: A Story...
Read MoreStudent Friendly Scanning Electron Microscopes
Recent Blogs Student Friendly Scanning Electron Microscopes For many manufacturers...
Read MoreRelated Product Categories
Industrial X-Ray Inspection Systems | NDT Equipment
Explore high-performance x-ray inspection systems for electronics, batteries, semiconductors, and...
Read MoreSEM’s: Tabletop & Compact Floor Standing
Unlock the full potential of high-performance tabletop SEM capabilities with...
Read MoreHigh Resolution Scanning Electron Microscopes for Advanced Research
Unlock the full potential of high-performance tabletop SEM capabilities with...
Read MoreAccessories and Lenses
Complementing our comprehensive instrument offerings, we provide a diverse range...
Read MoreMicroscope Cameras And Software
In the rapidly evolving world of microscopy, having the right...
Read MoreCompound Upright Microscopes
Compound microscopes for applications including education, materials manufacturing and research,...
Read MoreErgonomic Routine Stereo Microscopes
The standard in ergonomic microscopy. For users doing repeated rework...
Read MoreForensics Microscope
We offer a comprehensive range of forensic microscopy solutions designed...
Read MoreRoutine Inspection/Assembly Microscopes
Maximize quality control and achieve flawless assembly with our durable,...
Read MoreErgonomic Research Stereo Microscopes
Reproducible results are crucial in imaging, especially when capturing intricate...
Read MoreDigital Microscope
In the era of cutting-edge technology, digital microscopes have revolutionized...
Read More