Microtechnology
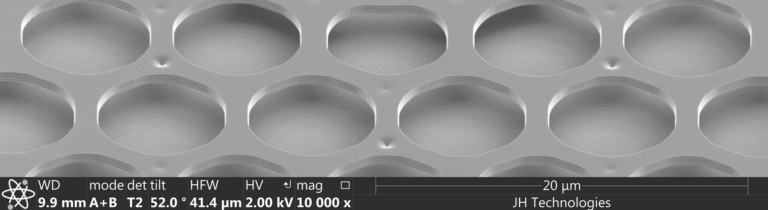
Microtechnology encompasses a wide array of applications involving microelectronic and micro-mechanical parts, and the assembly of those parts. This class of applications stretches across a wide swath of industries from defense and consumer electronics to telecommunications and photonics. Design verification, assembly, quality assurance, inspection, and defect analysis are segments in which customers need to see these devices. Today you are hard pressed to find a device that doesn’t have some microelectronic or micro-mechanical parts in it. Printed Circuit Boards or PCBs are everywhere.
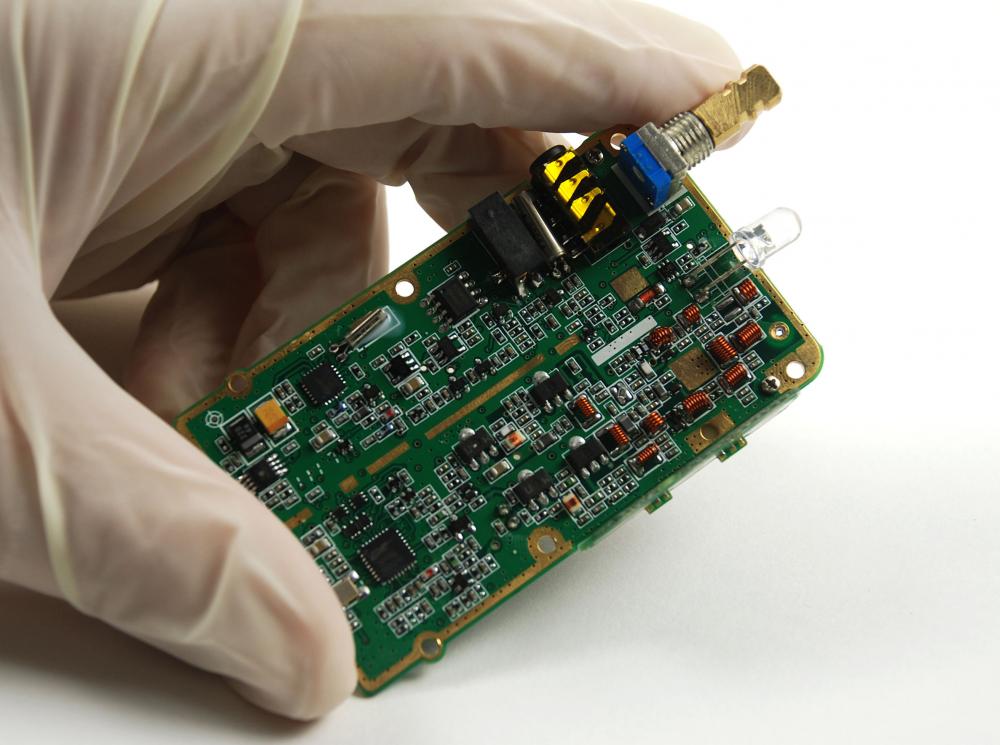
Related Blogs
Memory Device Cross-Sectioning [Learn from the JHA Team]
Recent Blogs Memory Device Cross-Sectioning [Learn from the JHA Team]...
Read MoreSolutions for Semiconductor Applications
Recent Blogs Solutions for Semiconductor Applications JH Technologies is pleased...
Read MoreBruker EDS & EBSD
Recent Blogs EDS & EBSD for SEM Adding Bruker EDS to your...
Read MoreNew S lynx 2 Optical Surface Profiler
Recent Blogs New S lynx 2 Optical Surface Profiler A...
Read MoreRelated Product Categories
Industrial X-Ray Inspection Systems | NDT Equipment
Explore high-performance x-ray inspection systems for electronics, batteries, semiconductors, and...
Read MoreSEM’s: Tabletop & Compact Floor Standing
Unlock the full potential of high-performance tabletop SEM capabilities with...
Read MoreHigh Resolution Scanning Electron Microscopes for Advanced Research
Unlock the full potential of high-performance tabletop SEM capabilities with...
Read MoreAccessories and Lenses
Complementing our comprehensive instrument offerings, we provide a diverse range...
Read MoreJH Analytical Services
Our analytical laboratory provides specialized testing and characterization services across...
Read MoreMicroscope Cameras And Software​
In the rapidly evolving world of microscopy, having the right...
Read MoreMetrology and 3D Surface Profiling
In the realms of scientific research, industrial inspection, and quality...
Read MoreCompound Upright Microscopes
Compound microscopes for applications including education, materials manufacturing and research,...
Read MoreErgonomic Routine Stereo Microscopes
The standard in ergonomic microscopy. For users doing repeated rework...
Read MoreSample Preparation
We understand the complexities involved in materials preparation and analysis....
Read MoreRoutine Inspection/Assembly Microscopes
Maximize quality control and achieve flawless assembly with our durable,...
Read MoreErgonomic Research Stereo Microscopes
Reproducible results are crucial in imaging, especially when capturing intricate...
Read MoreElectron Microscopy Sample Preparation
Preparing samples flawlessly is crucial for obtaining top-notch electron microscope...
Read MoreDigital Microscope
In the era of cutting-edge technology, digital microscopes have revolutionized...
Read More